2.5-Dimensionaler Druck eines rotationssymmetrischen Bauteils in den Raum
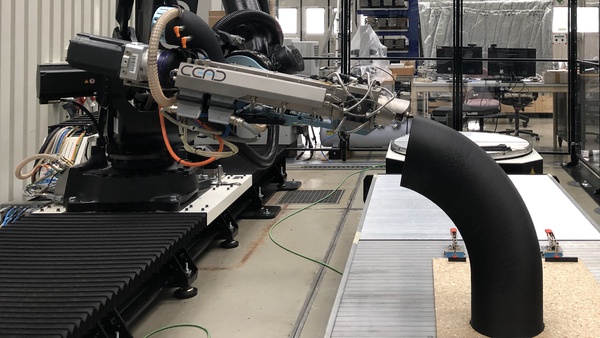
Großskalige additive Fertigungssysteme halten in den vergangenen Jahren immer mehr Einzug in industriellen und wissenschaftlichen Bereichen. Speziell für Polymer- und Kompositwerkstoffe wird hierbei das Materialextrusions (MEX) -verfahren, welches durch eine einfache Prozessführung gekennzeichnet ist, angewandt [1].
Analog zu den anderweitig eingesetzten additiven Verfahren, wie bspw. dem Selektiven Laser Sintern (SLS), sind die Bauteileigenschaften des gewünschten Endprodukts von verschiedenen Faktoren abhängig. Dazu zählt die durch den Prozess hervorgerufene komplexe thermische Geschichte und die dadurch resultierenden mikrostrukturellen Vorgänge [2]. Speziell bei semikristallinen Thermoplasten treten auf Werkstoffebene Vorgänge auf, die die makrostrukturellen Bauteileigenschaften positiv als auch negativ beeinflussen können. Als ein negativer Einfluss wären bspw. die thermischen Eigenspannungen zu nennen, welche infolge der Kristallisation auftreten und einen Schrumpf des Bauteils hervorrufen. Weiterhin können kristalline Strukturen, speziell im Verbindungsbereich zweier Extrudatstränge, die Diffusion von Molekülketten behindern und damit die Adhäsion senken. Die Konsequenz ist ein anisotropes Materialverhalten im Endprodukt [3].
Um den oben genannten Herausforderungen entgegen wirken zu können, sollen die auf Werkstoffebene auftretenden Vorgänge beschrieben und untersucht werden. Hierbei steht im Mittelpunkt des Projektes die Ausarbeitung und Validierung eines detaillierten Simulationsmodells zur Darstellung des MEX-Verfahrens und die Materialmodellierung der thermischen Kristallisation, welche in die Simulation eingebunden werden soll [4]. Außerdem sollen neben Variationen verschiedener Fertigungsparameter zusätzliche Peripherien, u. A. Heiz- und Kühlelemente, genutzt werden, um das Temperaturfeld im laufenden Prozess zu modifizieren [3].
Aus den gewonnenen numerischen Erkenntnissen sollen die makrostrukturellen Bauteilkennwerte abgeleitet und bestimmt werden. Weiterhin sind potentielle Fehlerquellen im großskaligen MEX-Verfahren vorab darstellbar, wodurch Zeit und Materialkosten gespart werden können.
Simulative Darstellung des MEX - Verfahrens
Mikrostrukturelle Untersuchungen in Bezug auf die thermische Kristallisation
Makrostrukturelle Untersuchungen
Demonstrator
Die in diesem Forschungsvorhaben gewonnenen Erkenntnisse sollen genutzt werden, um potentielle Fehler während des Fertigungsprozesses zu minimieren und die Bauteileigenschaften des Endprodukts vorhersagen zu können. Dabei soll der Schwerpunkt auf der Untersuchung der mikrostrukturellen Vorgänge, hier im Rahmen der Kristallisation, liegen. Mit den dabei erhaltenen Ergebnissen sollen Nutzende für großskalige MEX-Systeme mehr Sicherheit in der Gestaltung von Bauteilen und der richtigen Wahl von Fertigungsparametern erhalten.
Weiterhin soll eine Prozessverbesserung mittels zusätzlicher Peripherie erreicht bzw. untersucht werden. Mit den dabei eingesetzten Heiz- und Kühlelementen sollen gezielt gewünschte Bauteileigenschaften, neben der Wahl der Fertigungsparameter, eingestellt werden können. Der Druck und die Realisierung von Bauteilen mit geeigneten Bauteileigenschaften im tatsächlichen dreidimensionalen Raum soll langfristig erreicht werden.
Zusammengefasst dient diese Grundlagenforschung der Steigerung mechanischer Bauteileigenschaften der Endprodukte und der Verbesserung des Fertigungsprozesses.
Diese Forschungsarbeit wird durch dtec.bw – Zentrum für Digitalisierungs- und Technologieforschung der Bundeswehr gefördert. dtec.bw wird von der Europäischen Union – NextGenerationEU finanziert.